Origin Alliance – Safe Work Australia best workplace health and safety management system award
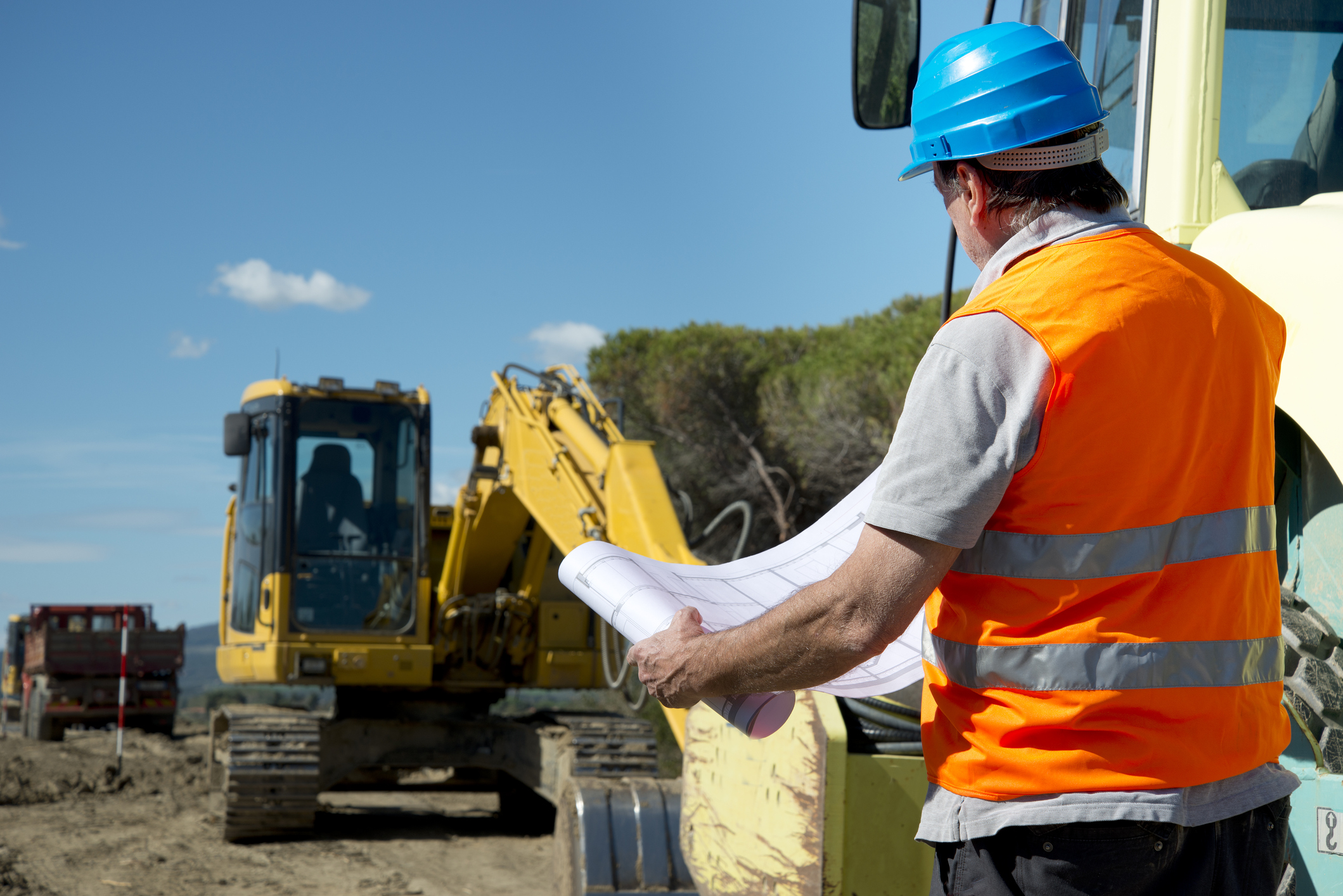
Background
Three companies accredited under the Australian Building and Construction WHS Accreditation Scheme (the Scheme) won the Safe Work Australia ‘best workplace health and safety management system’ award in April 2013 for their collaboration on the Ipswich Motorway Upgrade: Dinmore to Goodna (D2G) project. The Origin Alliance comprised Abigroup Contractors, Fulton Hogan and Seymour Whyte.
Located to the West of Brisbane, the federally funded $1.95 billion D2G project was opened on 15 May 2012. It was delivered six months early, and approximately ten per cent under budget. The project was considered one of the most complex road infrastructure projects ever undertaken in South East Queensland.
The D2G project aimed to provide a less congested and safer motorway, including increasing local road connectivity and functionality, access to public transport, and increasing and improving facilities for pedestrians and cyclists. A state of the art Intelligent Transport System was also installed to improve ongoing management of the motorway, and to provide increased driver safety.
These improvements were achieved by:
- Widening the existing motorway
- Adding new service roads
- Adding 24 kilometres of shared pedestrian and cyclist facilities
- Adding 26 new bridge structures
- Upgrading two motorway-to-motorway interchanges.
Safety Challenges
Alliance members report that the Origin Alliance had its own unique safety culture, vision and goals. Every employee understood what was expected of them, thus enabling the successful delivery of the D2G project safely, on time, and on budget.
Throughout the life of the project there were extensive safety challenges that needed to be addressed, including:
- The management of 1200 people
- Upgrading the Motorway under live traffic conditions
- Working in a narrow construction corridor
- Demolishing 13 existing bridges
- Removing more than 200 unexploded ordnance across the construction footprint due to parts of it being a former rifle range
- Dealing with the devastation caused by the January 2011 Queensland floods.
Addressing the Challenges
The key objectives of Origin Alliance’s approach to safety consisted of:
- Making everybody on site accountable for safety
- Training people so they understood what was at risk
- Equipping project leaders at all levels with the skills, knowledge and tools they needed to think and work safely
- Genuinely caring for people
- Enabling everybody on-site to do the little things well
- Creating a no blame culture.
When forming the Origin Alliance, the alliance partners all provided input into the project’s Workplace Health and Safety (WHS) Management System and safety culture. As a result, the Origin Alliance designed a plan for key safety behaviours to be adhered to on site. The Origin Alliance referred to these as the ‘Golden Rules’ and everybody who was inducted onto the D2G project was required to sign a ‘contract’ specifying that they would abide by these ‘Golden Rules.’ Ten thousand people were inducted onto the site over the life of the project.
The Origin Alliance wanted employees to work safely not because they had to, but because they wanted to. They instilled a culture whereby all workers on site had to embrace the ‘Origin Alliance Way’ of safety. They ensured that everybody on site was genuinely cared for, and received the right training, knowledge and tools to allow them to perform work safely.
A no blame culture was also created, encouraging people on site to speak up if they were being asked to undertake unsafe practices, or if they believed there were safer ways of performing tasks.
The Origin Alliance also tracked people’s commitment to—and understanding of—on-site safety requirements, by collecting information on their OHS Management Systems. They also monitored key lead and lag indicators regularly to identify any emerging safety trends. Origin Alliance stated that their aim was to ‘achieve a deeper level of analysis to identify long term trends and underlying reasons for incidents, injuries and near misses so it could continually improve its safety performance.’ Safety was always the first item on the agenda for meetings and if any issues arose, they were communicated ‘up the chain’ and minuted for action. ‘Lessons learnt’ documents were also created from safety incidents to ensure the same incident would not happen again.
Helpful advice for companies undertaking similar projects
Origin Alliance members believe that it is essential for a company to create an effective site culture at the very beginning to ensure projects are delivered safely and effectively, ‘creating a safety culture is not just about developing the right attitude and commitment to safety from everyone working on-site but also about ensuring that everyone on-site has the necessary skills, resources and support they need to do their job safely.’
As well as creating a safety culture, companies must also encourage employees and subcontractors to speak up if they are being asked to work in an unsafe manner, and to also report any incident, no matter how big or small.
Scheme Accreditation and the project
Accreditation under the Scheme has proved to be extremely beneficial to the Origin Alliance. Alliance members noted the Scheme was particularly useful when it came to things such as:
- Effective management of plant
- Development and implementation of D2G’s safety in design policies and processes
- Motivation to exceed safety requirements through audits.
The Alliance stated that ‘knowing an FSC audit would take place in 2010 was a huge motivating factor to ensure that Origin Alliance did not just meet its safety requirements but exceeded them where possible during the entire life of the project.’
Working together
The Alliance noted that a great example of how the Origin Alliance team worked together was during the January 2011 Queensland floods. The flood submerged the D2G project site and everything located on the ground floor was lost. They formed a flood recovery team and every person asked to participate gave a one hundred per cent commitment to recovering the project site and helping the local community. After the floods the local community and key stakeholders also saw the Origin Alliance as people that they could turn to for help. The Origin Alliance not only provided assistance with equipment and man power, but also served as people others could talk to. The Origin Alliance stated that:
‘The work undertaken by the Origin Alliance during the floods created an enormous amount of goodwill, support and respect within the local community and across other key stakeholders. It also created relationships based on trust within the community and across the Origin Alliance team. These relationships were a major contributing factor to the project being delivered under time and budget.’
Mentoring, team building and empowerment also played an important role in the Origin Alliance’s ability to work well together. Sharing new ideas and giving feedback on ways to work safely were also encouraged. These strategies helped the Alliance meet their deliverables, and were achieved by:
- Specific information sharing activities
- Activities designed to maintain Origin Alliance’s unique culture
- Activities designed to bring the Origin Alliance team together as often as possible
- Opportunities for people to provide feedback.
Mark Bingley, Safety Manager of the Origin Alliance added: ‘I believe the project has been a success because of the leadership that it has had and the way the culture has been developed and nurtured from day one. There really has been a strong commitment to the end goals, not just from a construction point of view but from across all aspects of the project. From day one, Mick O’Dwyer provided strong, visible, practical leadership, particularly in the application of our safety policy on a site-wide basis. As Alliance Manager, he personally applied the policy to everything he did on a daily basis. Mick truly believed the project could be delivered safely and he instilled this belief in everyone who worked with him.’
About these case studies
The Australian Government is committed to improving the WHS standards for all workers on building and construction projects.
These case studies have been developed to share practical ideas that can be adopted by industry to assist in their own management of WHS issues.
The Federal Safety Commissioner consults widely with industry, WHS authorities and other relevant agencies to promote a cooperative approach to improving WHS performance.
The vision of the Federal Safety Commissioner is a building and construction industry where no one is harmed.
For further information:
- Contact the FSC Assist Line on 1800 652 500
- Contact the OFSC via email at ofsc@dewr.gov.au
Disclaimer
The Office of the Federal Safety Commissioner has prepared this case study to promote workplace health and safety (WHS) in the Building and Construction Industry. When developing WHS initiatives, businesses and individuals should consider the circumstances and requirements particular to them, and seek professional advice where required.
While the Commonwealth has exercised reasonable care in providing useful information, the Commonwealth makes no representations, express or implied, as to the accuracy of the information contained in this case study. The Commonwealth accepts no liability for any use of the information contained in this case study or any reliance placed on it.
This case study may list persons, organisations, products, or services, or may incorporate material sourced from third parties. Such lists or material are assembled in good faith. However, any such list or material does not necessarily constitute any form of endorsement by the Commonwealth of that person, organisation, product, service, or third party. The Commonwealth does not accept any responsibility for such lists or material.