Bouygues Construction Australia
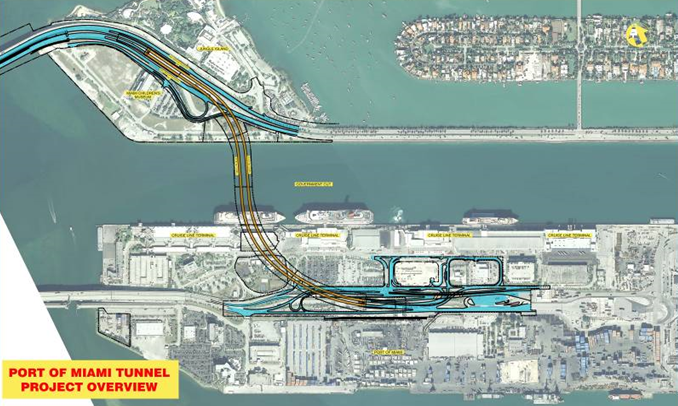
Multinational company hails FSC accreditation as best practise!
Bouygues Construction Australia, part of the massive French multi-national group Bouygues S.A. which reported sales of over €33 billion in 2013, has praised the Australian Government Building and Construction WHS Accreditation scheme (the Scheme), as representing global best practise in safety systems management.
The BYCA National QSE Director, Mr Ritchie Green said:
“The best practice BYCA safety systems that were developed in conjunction with the Federal Safety Commissioner (FSC) will now be rolled out to the English speaking countries in which Bouygues Construction operates.”
An ever increasing number of international companies are applying for and achieving accreditation under the Scheme. On 21 January 2014 Bouygues Construction Australia Pty Ltd (BYCA), the Australian arm of the international company Bouygues Construction, achieved FSC accreditation for the first time. In this case study BYCA shares their experience of achieving FSC accreditation and offers advice for other international companies considering becoming accredited.
Seeking FSC Accreditation and WHS Background
For BYCA, attaining FSC accreditation was a key strategic priority. It not only gives the company the opportunity to undertake major Commonwealth funded infrastructure projects, but will also help them build on their “local footprint” which has been established over the past 20 years through their work on major infrastructure projects.
BYCA’s current portfolio includes the Sydney to Airport Rail Link; Brisbane Hale Street Bridge; Glenfield Junction Alliance, Sydney; Landsborough Highway Upgrade, Queensland; and the North Strathfield Rail Underpass, Sydney.
BYCA have also been selected as preferred bidder in a 50:50 partnership with Lend Lease to design and build the NorthConnex link road in Sydney with a construction budget of $2.65 billion; and as part of the East West Connect consortium they have recently signed the finance, design and construct contract for Melbourne’s East West link project – a contract worth $6.8 billion.
For BYCA a commitment to health and safety is part of their approach to doing business which they call ‘Actitudes.’ The ‘Actitudes’ approach ensures all employees understand that health and safety is the company’s core organisational value, and empowers them to make positive decisions regarding their health, safety and welfare.
BYCA’s health and safety standards are underpinned by a safety cultural program that includes a senior management leadership inspection program, safety focus group, supervisor training program, and a focus on positive performance indicators.
According to Mr Green, aligning the company’s existing WHS Management System (WHSMS) with FSC criteria was consistent with the company’s safety strategy as the criteria focus on system elements that BYCA believes are critical to achieving positive safety outcomes. These include safety in design, risk management, and leadership commitment. Alignment to the FSC Evidence Guide also supports the company’s goal to maintain a lean and efficient WHSMS which is practical to implement at the coal face.
Furthermore, Mr Green said:
“The alignment of the BYCA WHSMS to FSC requirements provided our company Board assurance that our system had achieved an industry leading standard, something which makes the accreditation extremely worthwhile”.
Achieving FSC Accreditation
BYCA’s first step in the accreditation process was to perform a gap analysis to benchmark their International WHSMS against FSC Criteria.
Mr Green said that the company’s objective was “to retain our existing international system where practicable, and where required customise our system to meet requirements detailed in the FSC Evidence Guide, thus achieving uniformity in our business operations”.
Like all other companies, in order to achieve FSC accreditation BYCA was also required to undertake an on-site audit. A unique aspect regarding the BYCA audit was that it took place on an international project site, the Port of Miami Tunnel Project located in Miami, Florida, USA.
International Audit – Port of Miami Project
The Port of Miami Tunnel Project, valued at approximately $700 million (USD), connects MacArthur Causeway to Dodge Island, providing direct access between the seaport and highways I-395 and I-95.
Additionally, the Port of Miami tunnel is designed to improve traffic flow in downtown Miami and aid ongoing and future development in the area.
BYCA performed the design and construction of the two road tunnels, the construction of operation buildings, access ramps, connections to the port road network, ventilation, safety, surveillance, communication and fire-fighting systems, as well as relocation of the utilities affected by the project and an upgrade to the port's railway line.
An international audit presents unique challenges, and for BYCA the biggest of these was implementing their Australian WHSMS on a foreign site. This challenge was accentuated by the Port of Miami project being substantially underway, and the disparity between the United States and Australian legislative requirements. According to Mr Green, “the collaborative effort between the BYCA QSE Team and the Port of Miami Tunnel Project Team underpinned the success of the project audit. BYCA attaining FSC accreditation via a complex international audit also sets a precedent in the industry as only a small number of contractors have achieved this result with a single Project Audit.”
Design for a Global System
For Bouygues the audit undertaken at the Port of Miami project was also an important step toward achieving their goal of a Global WHSMS. The company intends to utilise BYCA’s WHSMS for operations in all English speaking countries around the world. The significant investment made in aligning Bouygues’ American and Australian WHSMS builds a platform for such a Global system while the attainment of FSC accreditation provides a ‘mandate’ to utilise the BYCA WHSMS.
According to Mr Green, this decision is due in part to the perception that the company’s Australian WHSMS is superior to other parts of the world, and provides Bouygues with the best opportunity to eliminate high consequence incidents. For BYCA aligning a Global system to FSC requirements ensures the company maintains an industry-leading system which is lean and efficient whilst maintaining operational continuity.
Advice to International Companies
BYCA offered the following advice to other international companies seeking accreditation:
- Make sure senior management are 100% committed to the accreditation process and proactively lead it. BYCA had commitment from their executive and senior management, including Managing Director Philippe Bouquet.
- Ensure your company’s WHSMS is streamlined, practical, and not overly onerous to implement, as the major goal of any system should be to support operational personnel meet their safety obligations.
- Ensure your safety team can effectively engage with project teams to help employees understand the tangible benefits of implementing an industry-leading WHSMS (e.g. reduced injury and illness rates, increased productivity, reduced legal exposure).
- Develop a WHSMS that invests a peak level of energy into managing potential Class 1 hazards including mobile plant, work at heights, cranes and lifting, energy isolation, electrical, utilities management, and temporary works.
- Implement positive performance indicators to measure the effectiveness of your WHSMS rather than relying solely on prohibitive zero harm regression targets.
According to Mr Green:
“The application of the above principles provides BYCA’s WHSMS a point of difference, and ensured our success in attaining FSC Accreditation.”
I want more information
Any international companies considering accreditation can find more information regarding the Australian Government Building and Construction WHS Accreditation Scheme and accreditation at: fsc.gov.au.
Companies can also contact the Office of the Federal Safety Commissioner on 1800 652 500 or at ofsc@employment.gov.au.
About these case studies
The Australian Government is committed to improving the WHS standards for all workers on building and construction projects.
These case studies have been developed to share practical ideas that can be adopted by industry to assist in their own management of WHS issues.
The Federal Safety Commissioner consults widely with industry, WHS authorities and other relevant agencies to promote a cooperative approach to improving WHS performance.
The vision of the Federal Safety Commissioner is a building and construction industry where no one is harmed.
For further information:
- Contact the FSC Assist Line on 1800 652 500
- Contact the OFSC via email at ofsc@dewr.gov.au
Disclaimer
The Office of the Federal Safety Commissioner has prepared this case study to promote workplace health and safety (WHS) in the Building and Construction Industry. When developing WHS initiatives, businesses and individuals should consider the circumstances and requirements particular to them, and seek professional advice where required.
While the Commonwealth has exercised reasonable care in providing useful information, the Commonwealth makes no representations, express or implied, as to the accuracy of the information contained in this case study. The Commonwealth accepts no liability for any use of the information contained in this case study or any reliance placed on it.
This case study may list persons, organisations, products, or services, or may incorporate material sourced from third parties. Such lists or material are assembled in good faith. However, any such list or material does not necessarily constitute any form of endorsement by the Commonwealth of that person, organisation, product, service, or third party. The Commonwealth does not accept any responsibility for such lists or material.